limitations of hardness testing|ceramic hardness testing : sourcing The Brinell hardness test is used for hardness testing larger samples in materials with a coarse or inhomogeneous grain structure. The Brinell hardness test (HBW) indentation leaves a relatively large impression, using a tungsten carbide ball. The size of the indent is read optically. Used for materials with a coarse or inhomogeneous grain .
Resultado da 8 de jun. de 2023 · How to Give Feedback by Asking Questions. Managers can read books, get trained, practice and plan, and still your employee may toss you something you don’t anticipate. But you can handle it. The key is asking good questions and really listening. When you give feedback, you .
{plog:ftitle_list}
Resultado da 2 de jan. de 2024 · 66% (3 votes) Video Details. Screenshots. Share. Comments (1) DonVito. Duration: 0:46 Views: 57K Submitted: 1 month .
Hardness testing does have some limitations and challenges that can affect the accuracy and repeatability of hardness results, some of which are listed below: It is necessary to have properly prepared the surface of the .
In this article, we briefly explained the importance and application, advantages and disadvantages of Rockwell hardness test. We also introduce the Rockwell test with different .Hardness testing within the realm of materials testing. Today, hardness testing is one of the most widely used methods in mechanical materials testing, especially for metals. On the one hand, this test method can be used to find .Mohs Hardness Test: This qualitative test ranks minerals based on their scratch resistance against standard materials with known hardness values. It’s commonly used in geology and mineralogy for mineral identification. These hardness testing methods serve various purposes, from quality control in manufacturing processes to material selection . Limitations of Hardness Testing for Deep Drawing Applications July 29, 2020. 0. . Of course, this resistance varies among material types, but hardness-test results also depend on the size, shape and .
The Brinell hardness test is used for hardness testing larger samples in materials with a coarse or inhomogeneous grain structure. The Brinell hardness test (HBW) indentation leaves a relatively large impression, using a tungsten carbide ball. The size of the indent is read optically. Used for materials with a coarse or inhomogeneous grain . Advantages and disadvantages. The advantage of Rockwell hardness testing is the relatively short testing time and good automation capability, as the measured values are determined directly from the indentation depth without optical measurement under a microscope. This process is therefore particularly suitable for automated production.These hardness tests can be categorized as macro and micro. All hardness testing methods lie under these categories. In this article, we will discuss hardness types, advantages, disadvantages, and applications. These things are important to understand as they have many consequences on the mechanism of indentation in the hardness testing methods.
what is hardness testing
Hardness testing is a vital process in many industries. Our guide explains everything you need to know about this crucial technique. From testing methods to the key applications, we cover it all to help you stay informed. . Traditional hardness measurement is only applicable to large-sized samples, not only due to limitations of the measuring .The Leeb method is a quick and portable hardness test method, which is determined by the ratio of rebound velocity to the impact velocity of a moving impact body. It is best applied to solid parts of the object for example casting and forgings. In the article, we include the advantages and disadvantages of Leeb method in details.Every hardness test has its own advantages and limitations. In this article, the Vicker hardness test with its significance, applications, advantages and disadvantages, is discussed. Several factors are described here for a good understanding of the hardness test. Hardness testing is a crucial aspect of metallurgy, as it provides valuable insights into a material’s mechanical properties and overall quality. There are various methods available for measuring hardness, each with its own set of advantages and limitations. In this blog, we’ll delve into the Vickers Hardness Test and discuss when it’s best to use this method over other .
This limitation requires different combinations of test force and indenter shapes to accommodate the hardness of all the possible materials to be tested. Scales Initially, 15 scales were created using a 10 kg preliminary force; 60, 100 or 150 kg total test forces combined with diamond; 1⁄16, 1⁄8, 1⁄4 and 1⁄2-inch diameter ball indenters .
The hardness of rubber and elastomers according to Shore is determined using test procedures standardized in compliance with ISO 48-4 or ASTM D2240.. In the Shore hardness test, the indentation depth is measured using a spring-loaded indenter made of hardened steel to indent the material/specimen.The indentation depth is a measurement for Shore hardness, that is .The Rockwell method is a static hardness testing method, which can be further characterised as follows: It is one of the standardised procedures (ISO 6508, ASTM E18). The process is used to test hardness in the macro range (test force >= 49.03 N), more precisely with a test force of 29.42 to 1471 N. It is a differential-depth method. The Rockwell Testing systems depend on the material that is being tested including the hardness, thickness, indentation positioning, and scale limitations on the materials that are being tested. The material being tested must be at least 10x thicker than the indentation that the Rockwell indentation is going to be when it is made of the material.The hardness test is preferred because it is simple, easy, and relatively nondestructive. Hardness is not a fundamental property of a material. Hardness values are . today, mainly because it overcomes the limitations of the Brinell test. The inventor, Stanley P. Rockwell, a Hartford, Connecticut, heat treater, used the
Hardness Testing (HT) is an NDT method used to measure hardness of materials and is performed on ferrous and non-ferrous materials, and various non-metallic materials. . in the test material from an application of a given force . Limitations of the Mohs Hardness Scale Limitations of the Mohs scale include its lack of precision and that fact that it is a potentially destructive test. For example, if you test a gemstone by seeing whether or not corundum . The Vickers hardness test, an offshoot of the venerable Brinell test, has been used since the early 1920s. Although the concept of using one test method to cover a wide range of materials hasn’t changed much in the last 90 years, upgrades to the equipment used to perform the test have expanded its use and accuracy. The Vickers hardness number is the load (test .
The Brinell hardness test, which is widely used in numerous industries, offers several unique advantages and some limitations that are crucial for accurate hardness measurement. To choose the most appropriate testing method for specific materials and applications, it is important to understand these factors. The hardness test is a way to assess the quality of a material, determine its properties, and evaluate its suitability for a specific application. What is Hardness Testing? Hardness testing is a mechanical test that measures a material’s resistance to indentation, scratching, or abrasion. The test is performed by applying a specific force on . Rockwell Hardness Testing Theory. Rockwell hardness testing has several indenter types which in turn require separate major loads (kg). Figure 1 reflects common Rockwell scales used and their corresponding major loads. Figure 1. When Rockwell hardness testing, a minor load of 10kg is applied to the indenter used on the material being tested.
All information about the Vickers hardness test Test procedure Sample request for the Vickers method Vickers hardness Hardness Discover now. . The Vickers method has the following disadvantages: The surface quality of the specimen must be good, because the indent is measured optically. .V. Limitations of Rockwell Hardness Test. With all the huge benefits of easy set-up and speed of testing and result acquisition that Rockwell hardness testing offers, its information will be incomplete without stating its limitations. One major limitation is the indenter travel which is often limited to 0.2mm or 100 Rockwell points.Good reference to surface finish. Click here. 6) Samples should be thick enough and with a sufficient surface absorption layer. If a D-type impact device is used, the thickness of sample must be greater than 1" ( 25mm) if not supported, and the surface absorption layer (surface-hardening layer) should not be less than 0.8mm.To accurately measure the hardness of the material, the .
Advantages and Disadvantages Of the Rockwell Hardness Test. The Rockwell hardness test is a widely adopted method for evaluating the hardness of materials, especially metals. It provides numerous advantages that have made it a preferred choice across various industries. However, it's crucial to acknowledge its limitations and potential drawbacks.The Brinell method is a static hardness testing method, which can be characterised as follows: It is one of the standardised procedures (ISO 6506, ASTM E10). The Brinell method has a test load range of 1 to 3000 kgf, which means that this method can be used for hardness testing in the low-load and, above all, macro ranges (conventional range). Hardness of material; Different types of defects in material; Shape of material; The relative position of a coil carrying alternative current and material; . Limitations of eddy current testing. It requires the proper size of the coil to maintain the sensitivity of instruments.
static hardness testing
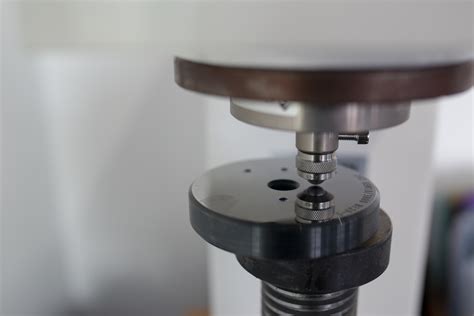
standards for hardness testing
Intelligent Tensile Tester maker
web21 de fev. de 2024 · RoboCop Rogue City Game Free Download Torrent. RoboCop Rogue City, you step into the metallic shoes of the iconic law enforcement machine, .
limitations of hardness testing|ceramic hardness testing